Abstract:Intergranular corrosion in welded stainless steel pipe can be prevented or minimized by taking specific measures during the welding process and throug
Intergranular corrosion in
welded stainless steel pipe can be prevented or minimized by taking specific measures during the welding process and through subsequent post-weld treatments. Intergranular corrosion occurs when the grain boundaries of the stainless steel become susceptible to corrosion due to sensitization, which is a result of chromium depletion at the grain boundaries. Here are ways to prevent or mitigate intergranular corrosion in welded stainless steel pipes:
Select the Right Stainless Steel Grade: Choose stainless steel grades with low carbon content, such as the "L" grades (e.g., 304L, 316L), which are specifically designed to be more resistant to sensitization and intergranular corrosion.
Low Carbon Welding Filler Material: Use welding filler materials with lower carbon content or matching the carbon content of the base metal to reduce the risk of introducing excess carbon during welding.
Control Heat Input: Minimize the heat input during welding to reduce the likelihood of sensitization. Lower heat input can help maintain the chromium content at the grain boundaries.
Preheat and Interpass Temperature Control: Implement preheating and interpass temperature control to minimize thermal stress and prevent sensitization. Preheating the base metal before welding and maintaining controlled temperatures between welding passes are essential.
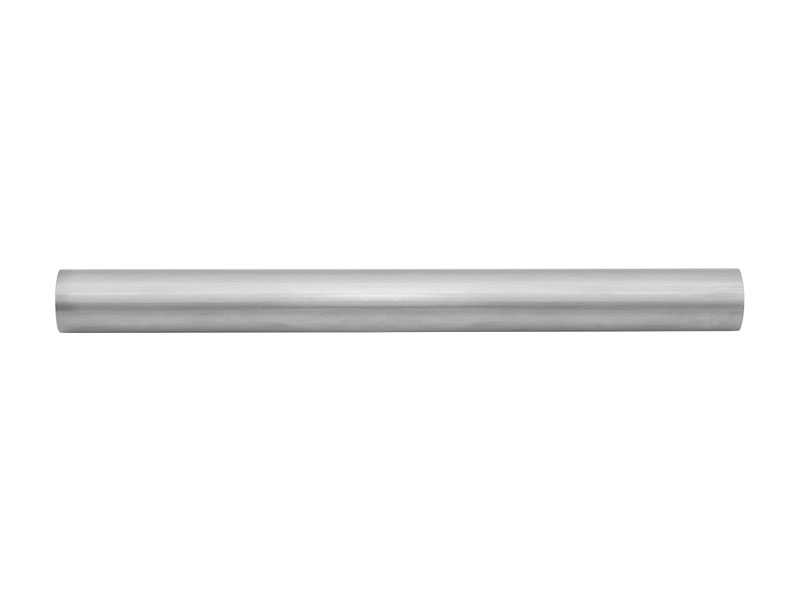
Welding Technique: Employ welding techniques that provide precise control of heat and minimize the time the stainless steel spends in the sensitization temperature range (usually around 800°C to 1500°C or 1472°F to 2732°F).
Post-Weld Heat Treatment (PWHT): Consider conducting PWHT if it's applicable for the stainless steel grade and the specific application. PWHT can help relieve residual stresses, reverse sensitization, and restore the corrosion resistance of the stainless steel. Follow recommended PWHT procedures and temperatures.
Use Nitrogen-Stabilized Stainless Steel: In applications where sensitization is a concern, consider using nitrogen-stabilized stainless steel grades, such as 304N or 316N. These grades contain nitrogen to help prevent sensitization and improve intergranular corrosion resistance.
Continuous Cooling: Ensure that the stainless steel cools rapidly through the sensitization temperature range to minimize the time it spends in that critical zone. Rapid cooling can help prevent chromium depletion at the grain boundaries.
Interpass Cleaning: Remove any contaminants, such as scale or oxides, between welding passes, especially if they have formed on the surface. Cleanliness is crucial to reduce the risk of sensitization.
Passivation: Perform passivation of the welded stainless steel pipe after welding to remove surface contaminants and promote the formation of a protective oxide layer on the surface, which can inhibit corrosion.
Avoid Sensitization-Prone Environments: In some cases, it may be practical to avoid placing welded stainless steel pipes in environments known to promote sensitization or intergranular corrosion. If possible, use alternative materials or protective coatings.
Quality Control: Implement rigorous quality control measures, including visual inspection, non-destructive testing (NDT), and metallographic examinations to detect and address any signs of sensitization or intergranular corrosion early in the welding process.
Consult with Experts: Seek advice from metallurgists, welding engineers, or corrosion specialists to ensure that the welding procedures, material selection, and corrosion prevention methods are optimized for the specific application.