Abstract:Non-destructive testing (NDT) is crucial for assessing the quality and integrity of welded stainless steel pipe without causing any damage to the pipe
Non-destructive testing (NDT) is crucial for assessing the quality and integrity of
welded stainless steel pipe without causing any damage to the pipes themselves. Various NDT methods can be used, depending on the specific requirements and the type of defect or flaw being investigated. Here are common NDT methods and steps for conducting NDT of welded stainless steel pipes:
Visual Inspection (VT):
Begin with a visual inspection to identify any obvious surface defects, such as cracks, discontinuities, incomplete weld penetration, or misalignment.
Use appropriate lighting, magnification tools, and inspection checklists to aid in the examination.
Liquid Penetrant Testing (PT):
Clean the surface of the welded stainless steel pipe to remove any contaminants or residues that might interfere with the test.
Apply a penetrant liquid to the surface, allowing it to seep into any surface cracks or defects.
Wipe off excess penetrant and apply a developer, which draws the penetrant out of the defects and makes them visible.
Inspect the surface for the presence of indications that reveal the locations of defects.
Magnetic Particle Testing (MT):
Clean the surface of the welded stainless steel pipe to remove any contaminants.
Apply magnetic particles to the surface, which will accumulate at the locations of surface or near-surface defects.
Expose the area to a magnetic field and inspect it under appropriate lighting conditions to reveal the indications of defects.
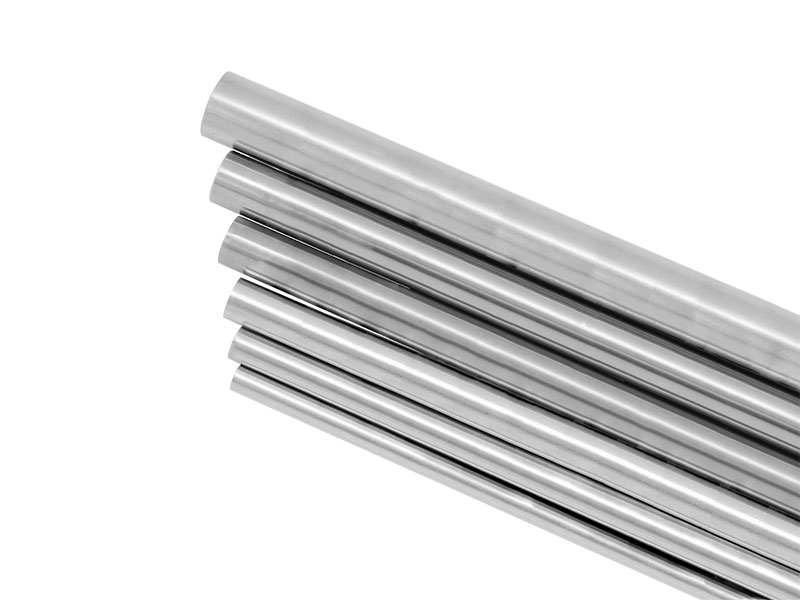
Ultrasonic Testing (UT):
Use an ultrasonic transducer that emits high-frequency sound waves and detects the echoes reflected from the internal and external surfaces of the stainless steel pipe.
Apply a coupling medium (usually a gel or water) to ensure good acoustic contact between the transducer and the pipe surface.
Interpret the ultrasonic signals to identify the presence, size, and location of internal or subsurface defects.
Radiographic Testing (RT):
Use X-rays or gamma rays to pass through the stainless steel pipe.
A film or digital detector on the opposite side records the variations in the radiation caused by the material thickness and the presence of defects.
The resulting radiographic image can reveal defects, such as porosity, lack of fusion, and cracks.
Eddy Current Testing (ET):
Pass an alternating current through a coil, creating an electromagnetic field.
The electromagnetic field induces eddy currents in the stainless steel pipe, and changes in the eddy currents are detected.
Eddy current variations can reveal defects, such as cracks, corrosion, and variations in wall thickness.
Radiographic Testing (RT):
Use X-rays or gamma rays to pass through the stainless steel pipe.
A film or digital detector on the opposite side records the variations in the radiation caused by the material thickness and the presence of defects.
The resulting radiographic image can reveal defects, such as porosity, lack of fusion, and cracks.
Eddy Current Testing (ET):
Pass an alternating current through a coil, creating an electromagnetic field.
The electromagnetic field induces eddy currents in the stainless steel pipe, and changes in the eddy currents are detected.
Eddy current variations can reveal defects, such as cracks, corrosion, and variations in wall thickness.
Ultrasonic Testing (UT):
Use an ultrasonic transducer that emits high-frequency sound waves and detects the echoes reflected from the internal and external surfaces of the stainless steel pipe.
Apply a coupling medium (usually a gel or water) to ensure good acoustic contact between the transducer and the pipe surface.
Interpret the ultrasonic signals to identify the presence, size, and location of internal or subsurface defects.
Radiographic Testing (RT):
Use X-rays or gamma rays to pass through the stainless steel pipe.
A film or digital detector on the opposite side records the variations in the radiation caused by the material thickness and the presence of defects.
The resulting radiographic image can reveal defects, such as porosity, lack of fusion, and cracks.
Eddy Current Testing (ET):
Pass an alternating current through a coil, creating an electromagnetic field.
The electromagnetic field induces eddy currents in the stainless steel pipe, and changes in the eddy currents are detected.
Eddy current variations can reveal defects, such as cracks, corrosion, and variations in wall thickness.
Acoustic Emission Testing (AE):
Acoustic emission testing detects and records stress-related, transient acoustic waves produced by the expansion or contraction of microstructural defects in the stainless steel pipe.
This method is often used for monitoring ongoing changes in the material.