Abstract:Stainless steel pipes can be joined together using various methods, including welding techniques. The specific welding technique you choose depends on
Stainless steel pipes can be joined together using various methods, including welding techniques. The specific welding technique you choose depends on factors such as the application, pipe thickness, and accessibility. Here are some commonly used welding techniques for joining stainless steel pipes:
TIG Welding (Gas Tungsten Arc Welding):
TIG welding is a popular technique for joining stainless steel pipes. It involves using a tungsten electrode to create an electric arc that melts the base metal and filler material (if needed). Inert gas, typically argon, is used as a shielding gas to protect the weld area from atmospheric contamination. TIG welding produces high-quality welds with excellent control over heat input and minimal distortion.
MIG Welding (Gas Metal Arc Welding):
MIG welding is another commonly used method for joining stainless steel pipes. It utilizes a consumable wire electrode and a shielding gas, such as argon or a mixture of argon and helium. MIG welding is faster than TIG welding and is suitable for thicker pipes. However, it may not provide the same level of precision and cleanliness as TIG welding.
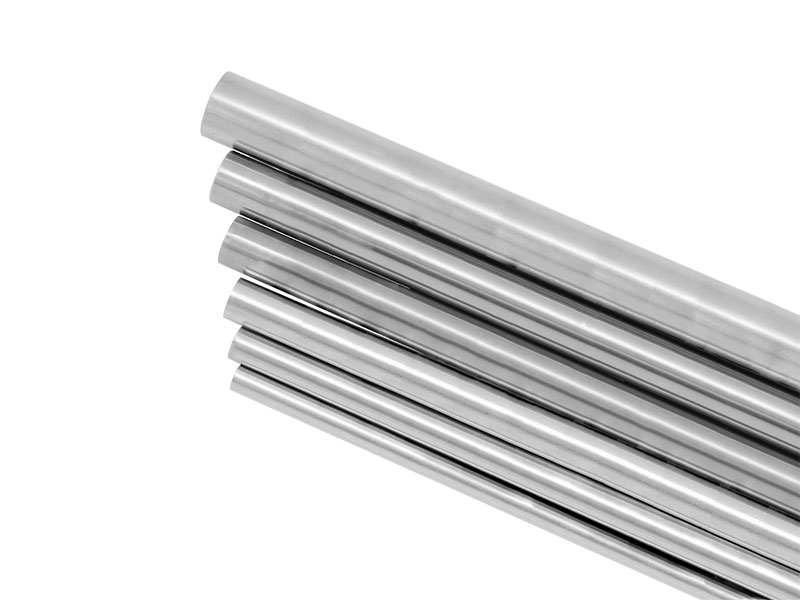
Stick Welding (Shielded Metal Arc Welding):
Stick welding involves using a coated electrode that provides both the filler metal and flux. This method can be used for joining stainless steel pipes, especially in outdoor or challenging environments. It is relatively simple and versatile but may result in more significant heat-affected zones and less control over the welding process compared to TIG or MIG welding.
Flux-Cored Arc Welding (FCAW):
Flux-cored arc welding is similar to MIG welding but uses a tubular wire filled with flux instead of a solid wire. This technique is often preferred for thicker pipes or in situations where wind or drafts can affect the shielding gas in MIG welding. It provides good penetration and deposition rates but may produce more spatter and require post-weld cleaning.
It's important to note that proper safety precautions should be followed when welding, including wearing appropriate protective gear, ensuring proper ventilation, and following recommended welding procedures.
For specific applications or critical joints, it is advisable to consult with a qualified welding professional or refer to industry standards and codes to determine the most appropriate welding technique and procedure for joining stainless steel pipes.